Fekete HSS-R és fényes HSS-G: Miért nem akar senki fekete fúrószárakat?
HSS-R fúrószárak fekete színűek – de ez nem jelenti azt, hogy automatikusan gyengébb minőségűek, mint szebb és fényesebb konkurensük, a HSS-G (1. ábra). A fekete fúrószárak rossz hírneve csupán rossz tapasztalatokon alapul. Az elmúlt évtizedekben a posztszocialista országokban a legfontosabb kiválasztási szempont az ár volt, ezért a piacot elárasztották az olcsó fúrószárak. Sok szakember azonban már felismeri, hogy az idejük értékes, és minőséges szerszámokkal szeretnének dolgozni. Emiatt választják inkább a „fényes” fúrószárakat.
De nem minden arany, ami fénylik – egy fényes fúrószár minősége akár egy „megcsavart szög” szintjén is lehet. Maga a szín és a kinézet nem kell hogy összefüggjön a minőséggel, gyakran csupán a felületkezelés módjáról van szó.
A spirálfúrószárakat nyugodt lelkiismerettel nevezhetjük „veteránoknak” – történetük egészen a 19. századig nyúlik vissza, mégis mind a mai napig a leggyakrabban használt betétszerszámok közé tartoznak fémek fúrásához.
Természetesen vannak különbségek a HSS-R és a HSS-G között, bár hőkezelésük teljesen azonos, és mérettartományuk is megegyezik (vagy nagyon hasonló).
Az általánosan elvárt minőségi követelmények a következők: fúrási sebesség (illetve a kis nyomóerő fúrás közben), élettartam (hosszú élezési intervallum – lassú tompulás), szívósság (törésállóság), univerzális felhasználhatóság különféle fémek fúrására. Ezek közül sok egymásnak ellentmondó tulajdonság, és nem könnyű őket megfelelően kiegyensúlyozni.

1. ábra. A HSS-R és HSS-G fúrószárak tipikus kivitele
Vizsgáljuk meg együtt, hogy a HSS-G fúrószár valóban minden követelményben „jobb-e”, mint a HSS-R. Röviden tekintsük át a három legfontosabb szempontot: a gyártási technológiát, az alapanyagot (amiből készülnek), a fúrószár csúcsának köszörülését.
HSS-R és HSS-G fúrószárak gyártási technológiája: alapvetően eltérő
A „R” betű a HSS-R fúrószáraknál a hengerelt (angolul Rolled, németül Rollgewalzt) eljárásra utal – pontosabban: a fúrószár funkcionális része hengerléssel, (melegalakítással) készül. Ez a folyamat az oka annak, hogy a funkcionális rész egyes méretei nem olyan pontosak, mint a HSS-G fúrószáraknál. A melegalakítás során azonban az anyag szálai tömörödnek és irányulnak, ami a fúrószár nagyon jó szilárdságában és fúrás közbeni stabilitásában mutatkozik meg.

2. ábra. A csúcsszög és a spirál dőlésszöge HSS-R fúrószár esetén
Egyszerűbben fogalmazva – a gyártási módszer ezeket a fúrószárakat “mindennapi kemény használatra” teszi alkalmassá. Ha a technológiai eljárást megfelelően betartják, és a kiindulási nyersanyag is megfelelő, akkor ezek a fúrószárak jól bírják a kemény fúrási körülményeket.
Ezért különösen alkalmasak elektromos kéziszerszámokkal történő fúrásra, mivel ellenállóbbak a töréssel szemben, ha a fúrószár megszorul – hiszen kézi fúráskor nem mindig biztosítható az abszolút merőleges vezetés a munkadarabban. Természetesen oszlopos fúrógépekben is használhatók.
A jellemző csúcsszögük 118°, és normál spirálszögű kialakítással készülnek (2. ábra), amely a legelterjedtebb és jó forgácselvezetést biztosít. Ezért széleskörű fúrási felhasználásra alkalmasak.
A HSS-R fúrószárak végső felületkezelése gyakran passziválás vagy nitridálás. Javul a keménység, jobban ellenáll a kopásnak, fáradásos igénybevételnek és a korróziónak is. Éppen ez a hasznos művelet adja a jellegzetes sötétszürke vagy fekete színüket – azt a színt, amit senki sem akar...
A technológia hátránya a kisebb furatpontosság – de ez kézi fúrásnál ritkán jelent problémát.
A „G” betű a HSS-G fúrószáraknál a csiszolt (angolul Ground, nnémetül Geschliffen) kivitelre utal. A csiszolt fúrószárak profilját automata gépeken alakítják ki egy előre hőkezelt (edzett) munkadarabból. A nagyobb átmérőket először marják. A csiszolás során a fúrószár átmérőjét is pontosítják, így geometriai méretpontosságuk sokkal nagyobb, mint a HSS-R fúrószáraké.
A HSS-G fúrószárak nemcsak 118°-os, hanem 130° vagy akár 135°-os csúcsszöggel is készülhetnek, így alkalmasak nagyobb szilárdságú acélok fúrására is – feltéve, hogy megfelelő minőségű alapanyagból készültek. Ennek a technológiának köszönhetően különböző spirálszögű fúrószárak is előállíthatók, bár a spirálszög (25°– 30°) a leggyakoribb (3. ábra).
Ott alkalmazzák őket, ahol pontos fúrásra van szükség. Fontos azonban, hogy a fúrógép orsója minimális ütéssel rendelkezzen, és ha lehetséges, gépi – egyenletes előtolású – fúrás történjen. Különösen ajánlott állványos és oszlopos fúrógépekhez. Kézi fúráskor sokkal hajlamosabbak a törésre, mint a HSS-R fúrószárak, ezért fúrás közben óvatosabb és finomabb kezelést igényelnek.
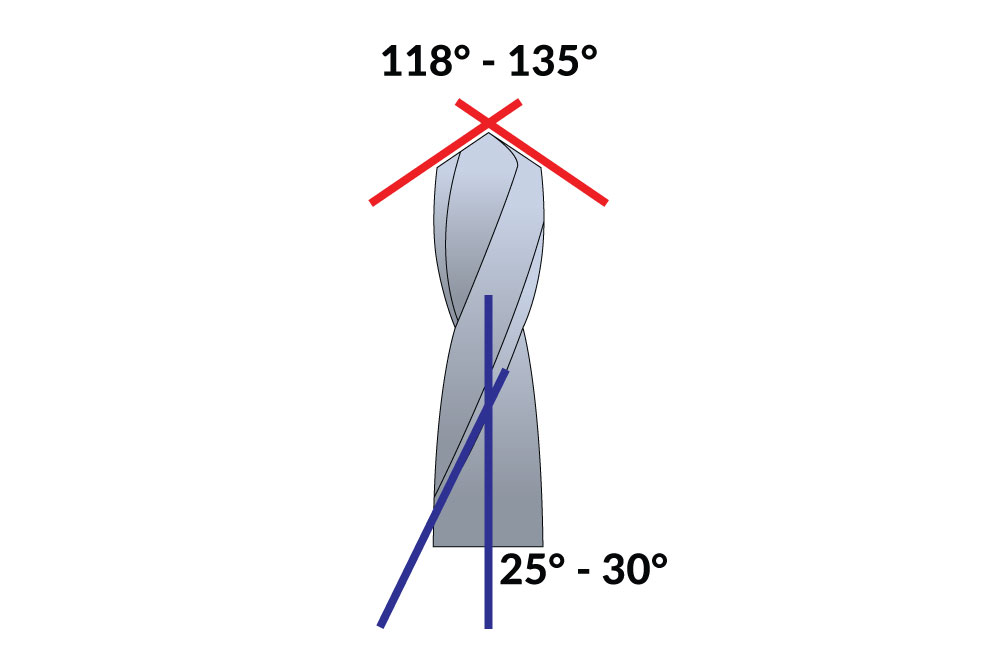
3. ábra. A csúcsszög és a spirál dőlésszöge HSS-G fúrószár esetén
A HSS-G fúrók általában nem rendelkeznek semmilyen felületi kezeléssel. Az ilyen gyártási technológia eredményeként nagyon szépek, és korrózió ellen megfelelő konzerváló anyagokkal kezelik őket.
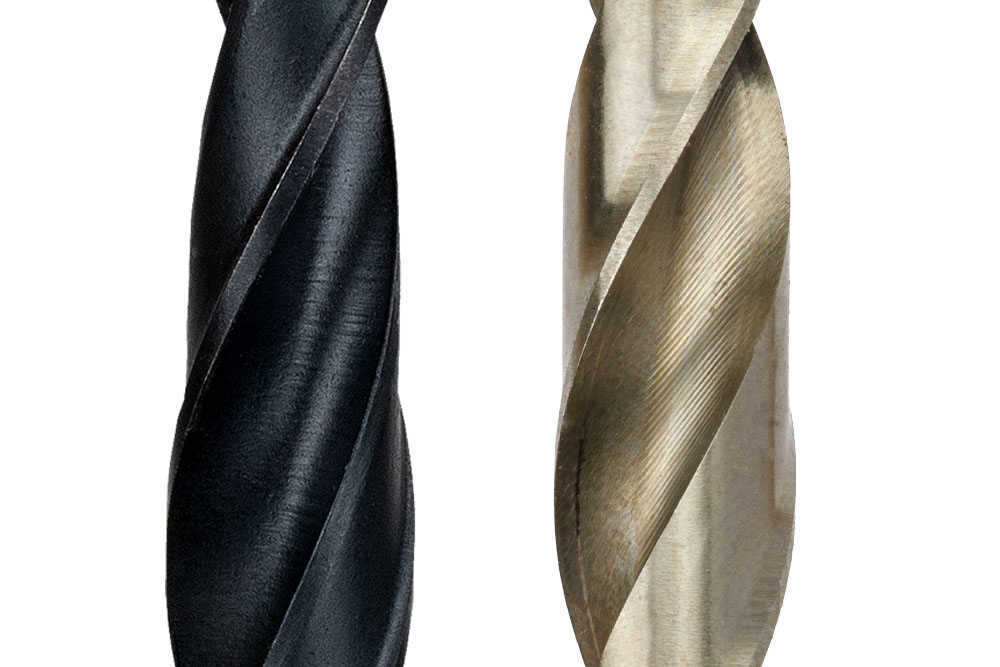
4. ábra. Spirál kialakítása: sima (HSS-R) és köszörülési nyomokkal (HSS-G)
Bár hozzászoktunk ahhoz, hogy a HSS-R és HSS-G fúrószárakat színük alapján különböztessük meg, léteznek "technológiai trükkök" is, amelyekkel a hengerelt fúrók felülete meglehetősen fényessé tehető. Kétségek esetén a csiszolási nyomok a legmegbízhatóbb megkülönböztető jelek - a HSS-R fúrószárnál a spirál felfutása a száron teljesen sima, a HSS-G fúrószárnál pedig jó fényviszonyok mellett csiszolási nyomok láthatók (4. ábra).
Zárszó: a HSS-R fúrószárak keményebbek, kevésbé törékenyek, de a HSS-G fúrószárak pontosabbak. Végül, de nem utolsósorban a HSS-R fúrószárak előnye az alacsonyabb ár is, ami a költséghatékonyabb gyártási és megmunkálási módszernek köszönhető - az előállítási költségek a HSS-G-hez képest ugyanazon nyersanyag felhasználásával több mint 25%-kal alacsonyabbak.
A HSS-R és HSS-G fúrószárak alapanyaga
Korábban a HSS-R fúrószárakat szerszámacélból is gyártották – manapság azonban minden HSS-R és HSS-G fúrószár gyorsacélból (HSS – High Speed Steel) készül. A név a vágási sebességből ered, amely 3-4-szer nagyobb, mint a szerszámacélé, amelyhez hasonlít. Az ötvözetlen szerszámacél azonban már 200°C-os hőmérsékleten elveszíti keménységét, ezért nem alkalmas fémre való fúrószárak gyártására.
A gyorsacél a magasan ötvözött acélok csoportjába tartozik. Alapvető összetevője a szén, azonban a fúrószár végső tulajdonságaira jelentős hatással vannak egyéb ötvözőelemek is – leggyakrabban volfrám (W), molibdén (Mo), króm (Cr), vanádium (V) és kobalt (Co). Megfelelő kombinációjukkal a fúrószárak tulajdonságai akár 500–600°C-ig, kivételes esetekben pedig akár 1000°C, vagy magasabb hőmérséklet fölött is megőrizhetők.
A leggyakoribb anyagokat, amelyekből a spirálfúrószárak készülnek, az 1. táblázat tartalmazza. A teljesség kedvéért itt feltüntettük az M42 anyagot is, amelyből 8% kobaltot tartalmazó fúrószárak készülnek, valamint az M35 anyagot, amelyből 5% kobalt tartalmú HSS-E fúrószárak gyártása történik.

1. táblázat. HSS anyagok és összetételük (az AISI szerint)
A HSS-R és HSS-G fúrószárak gyártására elsősorban a 4241, 4341 és M2 anyagok szolgálnak.
A fő összetevő, amely a fúrószár hőállóságát növeli, a volfrám. Minél több van belőle, annál jobb. Például az M2 anyag körülbelül háromszor annyi volfrámot tartalmaz, mint a 4241 anyag, ezért jobban tűri a magasabb hőmérsékletet, és kisebb szünetekkel lehet vele fúrni. Természetesen emellett alacsonyabb hűtési igénye is van a fúrás során.
A kiinduló nyersanyag összetétele rendkívül fontos, ezért megdöbbentő, hogy kevés gyártó tünteti fel, milyen anyagból készült egy adott fémre való fúrószár. A termékleírásokban általában csak a „kiváló minőségű gyorsacélból készült” kifejezést találjuk – de hogy pontosan milyen összetétele van és milyen minőségre lehet számítani - az csak nagyon ritkán derül ki.
Zárszó: mindkét fúrószár gyorsacélból készül – azonban annak összetétele eltérő lehet. Így könnyen előfordulhat, hogy egy szép, fényes HSS-G fúrószár alacsonyabb minőségű HSS acélból készült. Ha ez nincs feltüntetve a műszaki adatlapokban vagy a termékleírásokban, soha nem fogja megtudni. Kérdezze meg beszállítóit...
Élezés
A HSS-R fúrószár standard élezéssel készül (kúpos síkokkal – a DIN 1412 szabvány szerinti N Forma), amely megfelel az általános fúrási körülményeknek (5. ábra).
Előnye a masszív fő él, amely ellenáll az ütéseknek és az axiális erőknek. Az újraélezés kopás után egyszerű – némi gyakorlattal akár kézzel is élezhető. Széles körű felhasználásra alkalmas. Hátránya, hogy a széles keresztél nagy radiális erőt igényel fúrás közben.
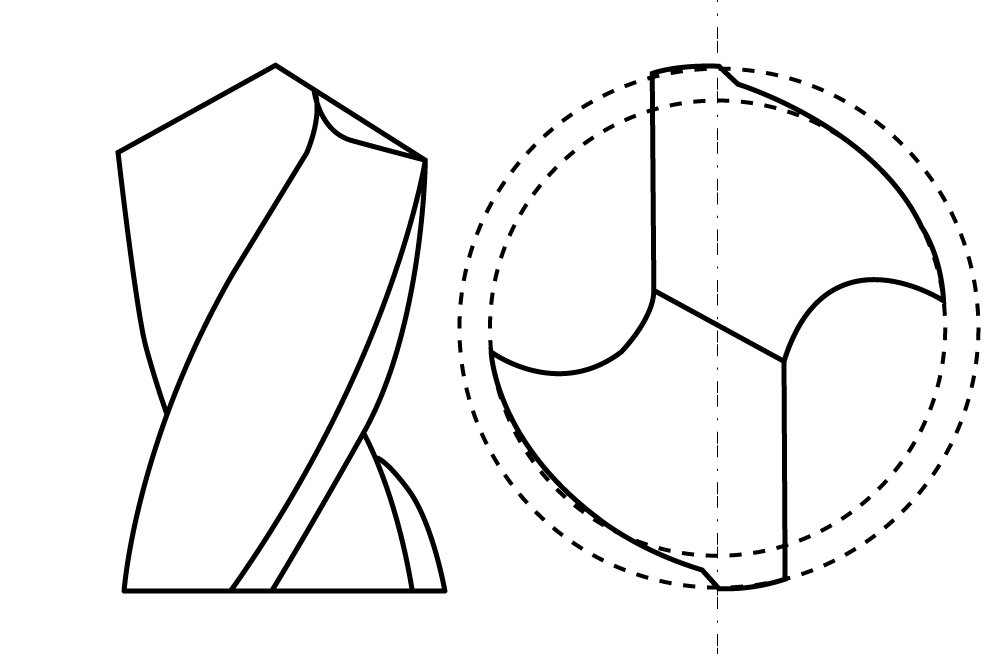
5. ábra. Standard élezés kúpos felületekkel: N Forma
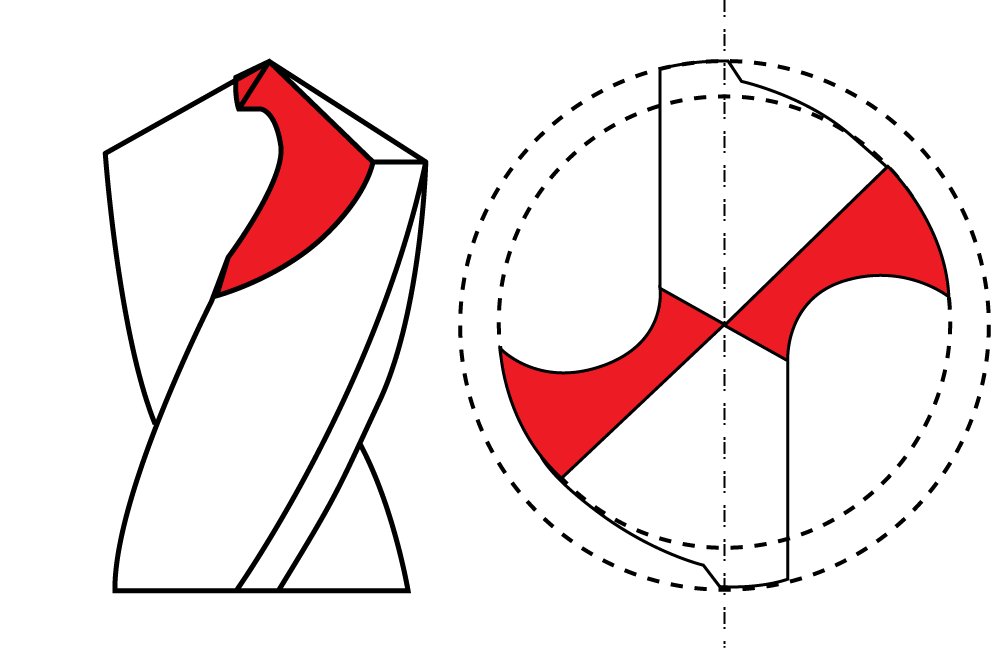
6. ábra. Keresztélezés a DIN 1412 szabvány szerint, C Forma
A HSS-G fúrószár lehet „csak” standard élezésű, de más élprofilt is kaphat. A legelterjedtebb a C Forma szerinti keresztélezés a DIN 1412 szabvány szerint – más néven „split point” (6. ábra).
Előnye, hogy kiváló központosítást biztosít, különösen a fúrás kezdetén, valamint kisebb előtoló erőt igényel – fúrás közben kevesebb nyomás szükséges. Különösen szívós és kemény anyagokhoz, valamint mély furatok fúrására alkalmas. A keresztélezést általában 3mm átmérőtől, ritkábban 2mm-től végzik. Az ilyen kis átmérőjű fúrószárakat kézzel élezik, ami „művészetnek” számít.

7. ábra. HSS-R és HSS-G – figyelje meg a csúcs alakját
A C formájú keresztélezés hátránya, hogy a tompa fúrószárak tökéletes újraélezése csak gépi köszörüléssel érhető el. Kézi élezésre csak kevesen képesek megfelelően.
Zárszó: A HSS-R fúrószárakat általában kúpos felületekkel rendelkező standard élezéssel gyártják, amely masszív, tartós és kopás után könnyen újraélezhető. Hátránya, hogy nagyobb nyomóerőt igényel fúrás közben.
A HSS-G fúrószárak gyakran szintén standard élezésűek, ezért téves az a feltételezés, hogy egy fényes HSS-G fúrószárnak automatikusan „split point” keresztélezése van. A keresztélezés technológiailag összetettebb, mint a standard változat, ezért az ilyen fúrószárak drágábbak.
HERMAN HSS-R és HSS-G fúrószárak: melyik a jobb?
Mindkét fúrószár típusunk - a HSS-R és a HSS-G - azonos csúcsszöggel (118°) és spirálszöggel (30°) rendelkezik. Közönséges szilárdságú acélok fúrására tervezték őket. Különböző alapanyagúak, és különböző a csúcs élezésük.
Tesztünkben azonos átmérőket (2x Ø3,0mm és 2x Ø6,0mm) hasonlítottunk össze, amelyekkel ugyanazzal az asztali fúrógéppel (teljesítmény 1550W), azonos sebességgel, azonos munkadarabba (közönséges lapos acél) fúrtunk, azonos előtoló nyomás mellett.
A fúrószárakat véletlenszerűen választottuk ki a teszthez egy több ezer darabból álló készletből.
Úgy választottuk ki a teszt helyszínét, hogy - ha szeretné - a saját körülményei között is ellenőrizhesse mért eredményeinket.
Arra összpontosítottunk, hogy azonos körülmények között összehasonlítsuk a fúrási sebességet, és azt, hogy a hegy fokozatos tompulásával hogyan növekszik a furat kifúráshoz szükséges idő.
Az időt mindig akkor mértük, amikor a fúrószár új (használatlan) volt az első fúráskor, majd minden ötven fúrás után. Minden tíz lyuk után 20 másodpercig üresjáratban hagytuk járni a fúrót befogott fúrószárral, hogy az egy kicsit lehűljön - de mindegyik fúrószárnál egyformán. Szándékosan nem használtunk vágó- vagy fúróolajat, hogy ne szülessenek körülötte lényegtelen viták. Meg akartuk nézni, hogy a HSS-G fúrószárak gyorsabban fúrnak-e, mint a HSS-R fúrószárak, és hogy milyen mértékben kopnak.
Tekintse meg a teszt helyszínén készült rövid videót.
Videó: A HSS-R és HSS-G fúrószárak összehasonlítása
A teszteredmények a következők:

Kiértékelés
A vizsgálati eredményekből több olyan következtetés is kitűnik, amelyek megerősítik az ebben a dokumentumban szereplő valamennyi technikai magyarázatot. A lényegesek a következők:
Ø3,0mm:
HSS-R: újként 7,5s alatt fúrta ki a lyukat, 300 lyuk után a fúrási idő kb. 12%-kal 8,4s-ra nőtt. A minden ötven fúrás után végzett összes mérés átlagos ideje 7,89s volt.
HSS-G: újként 4,2s alatt fúrta ki a lyukat, 300 lyuk után a fúrási idő kb. 19%-kal 5,0s-ra nőtt. A minden ötven fúrás után végzett összes mérés átlagos ideje 4,5s volt.
A HSS-R fúrószár fúrási ideje majdnem kétszerese volt a HSS-G fúrószár fúrási idejének. Itt érdemes elgondolkodni azon a kérdésen, hogy egy Ø3,0mm-es furat 8 másodperc alatt történő kifúrása valóban olyan sok-e kézi fúrás esetén. Ha a nyomást 1,9 kg-ról magasabb értékre emelnénk, a HSS-R fúró gyorsabban fúrna, de nem tudnánk fenntartani ugyanazokat a feltételeket - a HSS-G fúró nem bírná a megnövekedett nyomást ilyen kis átmérőnél, és a törés veszélye állna fenn. Mindkét fúrónál azonban 300 fúrt lyuk után csak enyhe élkopás volt tapasztalható, mivel a fúrási idő nem nőtt meg jelentősen - a teszt elején és végén mért kevesebb mint egy másodperces különbség jelentéktelen.
Ø6,0mm:
HSS-R: újként 9,7s alatt fúrta ki a lyukat, 300 lyuk után az idő kb. 77%-kal 17,2s-ra nőtt. A minden ötven fúrás után végzett összes mérés átlagos ideje 12,47s volt.
HSS-G: újként 9,7s alatt fúrta ki a lyukat, 300 furat után az idő majdnem a duplájára, 15,2s-ra nőtt. A minden ötven fúrás után elvégzett összes mérés átlagos ideje 11,01s volt.
A fúrás időbeli különbsége ennél az átmérőnél közel sem volt olyan jelentős, mint a 3,0mm-es átmérőnél, ami a fúrás során fellépő meglehetősen jelentős előtolási erővel magyarázható. Ebben az esetben megengedhettük magunknak - a 6,0mm-es átmérő sokkal kevésbé érzékeny az előtolási erőre, mint a kisebb átmérők, még a HSS-G esetében is.
Sokkal jelentősebb volt azonban a kopás mindkét fúrószárnál. A HSS-G jobban kopott, mint a HSS-R, bár végül a HSS-G még mindig gyorsabb volt, mint a HSS-R.
Zárszó
Egy mondatban: joggal lehetünk büszkék a fémre való fúrószáraink minőségére! Végül is mindegyik 300 lyukat fúrt, és még nem került olyan állapotba hogy kidobják - nézze meg a Ø6,0mm-es fúrószárak vágóélét a tesztelés előtt és után (8. ábra). A HSS-G fúrószáron látható a vágóél túlmelegedése. A HSS-R bizonyára szintén túlmelegedett, de itt ezt „elfedte” a fekete színe. Ebből is látható, hogy a vágó- és fúróolaj használata segített volna...

8. ábra. A HERMAN HSS-R és HSS-G fúrószárak élei: újonnan és 300 fúrt lyuk után
Van még itt egy fontos tény, amit tudatosítani kell - a fúrószárak átmérőjének a kétszeresére növelése azt jelenti, hogy a kifúrt térfogat kb. 4-szeresére nő (ezt ellenőrizheti, ha kiszámítja a fúrt lyuk térfogatát) - így a Ø6,0mm-es fúrószár jelentősen nagyobb kopása a Ø3,0mm-es fúrószárhoz képest természetes.
Gyakorlati tesztek azt mutatták, hogy a HSS-G fúrószárak gyorsabban fúrnak, mint a HSS-R fúrószárak, mégis a kéziszerszámokkal történő kézi fúráshoz a HSS-R fúrószárak előnyösebbek, mivel lényegesen ellenállóbbak a töréssel szemben, és ebből a szempontból sokkal többet kibírnak, mint a HSS-G fúrószárak.
És az élettartamuk is - ha kellően jó minőségű anyagból készülnek - nagyon elfogadható. És ne felejtsük el, hogy az áruk feleannyi.
A teszteléssel ugyanazokatt a feltételeket biztosítottuk, de a leghatékonyabb fúráshoz más fontos szempontokat is figyelembe kell venni, mint például az ajánlott vágási sebességet, amely a fúrógép fordulatszámával, a fúrandó anyag összetételével stb. függ össze. De ezek olyan területek, amelyekkel később foglalkozunk.
Most lehetősége van ingyenesen kapni egy HSS-R és HSS-G fúrókészleteket 20.000 Ft (ÁFA nélkül) vásárlás esetén, csak írja be a FURO jelszót a kosárban található megjegyzés mezőbe. Hasonlítsa össze őket, és fedezze fel mindkettő előnyeit.
Kulcsszavak: fúrószárak, HSS-R, HSS-G, fúrás, gyorsacél, minőség, tartósság, pontosság
Források:
A HERMAN cég belső műszaki és oktató dokumentációi
Petr Šindelář –
Velmi praktické a potřebné informace o vrtácích. Je dobré vědět jaký materiál na co použít.
Nagyon praktikus és szükséges információk a fúrókról. Jó tudni, hogy mihez milyen anyagot kell használni.
Lefordítani a szöveget Eredeti szöveget mutatniLukáš –
Pekný jednoducho napísaný praktický článok s príkladným testom a zaujímavou ilustráciou.
Szép, egyszerűen megírt gyakorlati cikk, példaértékű teszttel és érdekes illusztrációval.
Lefordítani a szöveget Eredeti szöveget mutatni