Kerámia csiszolóanyag - jó és nagy teljesítményű, de megéri?
A kerámia csiszolóanyagok, amelyek egyedülálló tulajdonságaikkal az anyagmegmunkálás határait feszegetik, első kereskedelmi felhasználására már 35 évvel ezelőtt sor került. Azonban csak az utóbbi években váltak szélesebb körben elterjedté. Lassan, de biztosan hatol be a szélesebb szakmai közvélemény tudatába. A kerámia csiszolóanyagok (1. ábra) így kiegészítik a hagyományos, jól ismert technológiákat, mint például a szintetikus korund (alumínium-oxid), a cirkónium-dioxid és a szilícium-karbid csiszolóanyagokat, elsősorban a legmagasabb minőségű termékcsoportokban.
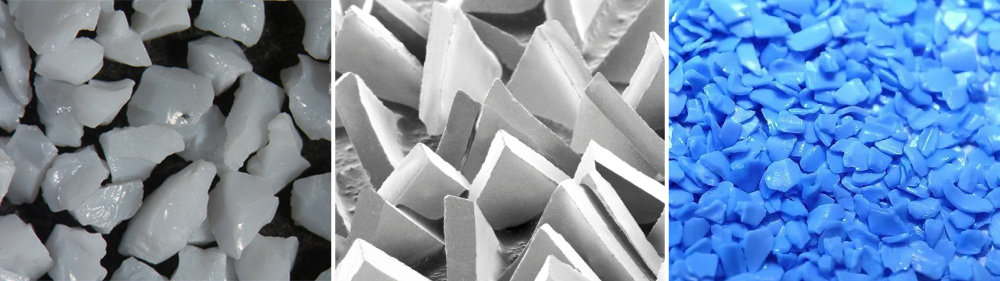
1. ábra. A kerámia csiszolóanyagok különböző változatai (alumínium oxid kerámia)
A kerámia csiszolóanyagok forradalmat jelentenek az iparágban. Bár a kémiai összetétel szintén korund, kis mennyiségű különböző adalékanyagokkal, a fontos különbség az anyag belső kristályszerkezetében van. A hagyományos csiszolóanyagokhoz képest ennek a nyersanyagnak az előállítása lényegesen összetettebb. A hagyományos szintetikus korundot nagy elektromos ívkemencékben állítják elő, ahol az alumínium oxidot magas hőmérsékleten ( 2000 °C-on) megolvasztják. Az olvadék lehűlésekor egy nagyon kemény anyag - szintetikus korund - keletkezik. A következő fázisban ezt különböző szemcseméretű granulátummá őrlik, amely a különböző abrazív betétszerszámok vagy hordozóanyagra felvitt csiszolóanyag betétszerszámok gyártási alapanyaga. A kerámia csiszolóanyagokat viszont az alapanyagok vékony porított rétegeinek magas hőmérsékleten történő szinterezésével állítják elő. A szinterezés során szilárd mikroszerkezet alakul ki, amely molekuláris szinten erősebb kötésekkel rendelkezik, ami a keletkező anyag nagyobb sűrűségét és fajsúlyát eredményezi. Ez a korundhoz képest nagyobb keménységet eredményez. Ez az előállítási folyamat elvileg nagyon hasonló a keményfém lapkák porkohászati előállításához.
A bonyolult gyártási folyamat következtében a kerámia csiszolóanyagok ára jelentősen magasabb, aminek szükségszerűen tükröződnie kell a végtermékek - vágó- és csiszoló betétszerszámok - árában. Mint minden új termék esetében, az ár az idő múlásával és a kereslet növekedésével fokozatosan csökken. 5 évvel ezelőtt egy tonna kerámia csiszolóanyag 17 000 euróba került - ma az emelkedő energiaköltségek ellenére ez az ár körülbelül 7500 euró. Összehasonlításképpen, egy tonna szintetikus korund körülbelül 1300 euróba kerül, és az elmúlt öt év során 30%-kal emelkedett a nyersanyag- és energiaárak emelkedése miatt. Így ez a prémium termék egyre megfizethetőbbé válik, és ma már nem talál olyan csiszoló betétszerszámot, amelyet ne lehetne megvásárolni kerámia csiszolóanyagú változatban is.
A szupercsiszolóanyagokat (gyémánt, CBN stb.) figyelmen kívül hagyva, amelyek gyártástechnológia és felhasználási terület szempontjából teljesen más iparágat képeznek, elmondhatjuk, hogy az aluínium oxid kerámia szemcsék rendelkeznek a leghosszabb élettartammal és a leggyorsabb anyagleválasztással az összes általánosan használt csiszolóanyag közül. Folyamatosan és agresszívan lehet velük dolgozni mind mérsékelt, mind magas munkadarabnyomás mellett. A kerámia csiszolóanyagok színe leggyakrabban fehér vagy halványkék, és a kerámia csiszolóanyagok színkódolásához a piros színt fogadták el (2. ábra).
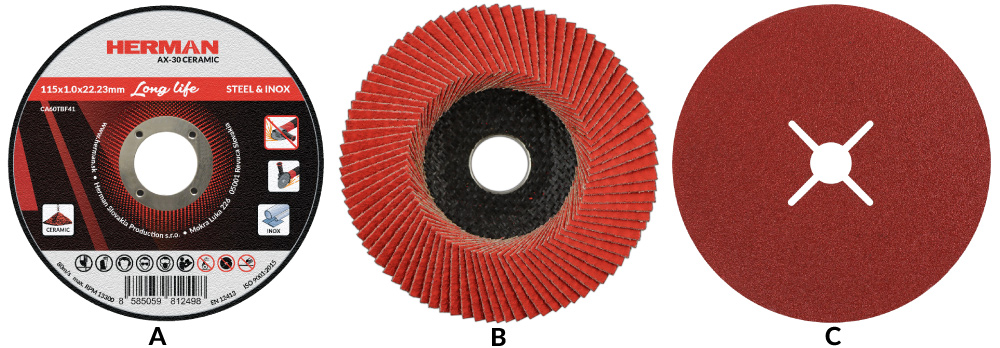
2. ábra. kerámia csiszolóanyagból készült vágó (A), lamellás (B) és fíber csiszoló tárcsa (C)
A kerámia csiszolóanyagok számos alapvető előnnyel rendelkeznek a korunddal szemben:
- nagyobb keménység és élettartam. A kerámia csiszolóanyag keményebb mint a korund, ami azt jelenti, hogy tovább bírja a kemény anyagok, például acél, rozsdamentes acél vagy ötvözött acélöntvény csiszolását. Ez a keménység hosszabb szerszámélettartamot és kevésbé gyakori szerszámcserét tesz lehetővé
- a mikrokristályos szerkezetnek köszönhetően képes hosszabb ideig megőrizni a csiszolószemcsék élességét
- alacsonyabb csiszolási és vágási hőmérséklet - a megmunkálás során kevesebb hő keletkezik, ami kevesebb túlmelegedést és a munkadarab tulajdonságainak jobb megőrzését jelenti
- hatékonyabb/gyorsabb anyagleválasztás a megmunkálás során
A kerámia csiszolóanyagoknak azonban vannak hátrányai is:
- magasabb ár
- ridegség: bár keményebbek, de a kerámia csiszolóanyagok törékenyebbek, mint a korund
Ez a csiszolóanyag univerzálisan alkalmazható, de tulajdonságai miatt elsősorban a legigényesebb ipari alkalmazásokban használják rozsdamentes acélok és szuperötvözetek megmunkálásához.
A hagyományos és a kerámia csiszolóanyagok közötti legjelentősebb különbség e csiszolóanyagok kopási módjában rejlik:
- a hagyományos csiszolóanyagok hajlamosak arra, hogy tompuljanak esetleg véletlenszerű irányokban elhasadjanak (3. ábra)
- a kerámia csiszolóanyagok finom mikrokristályos szerkezetűek, és az apró részecskék fokozatos letöredezése és elszabadulása révén az él éles marad (4. ábra)
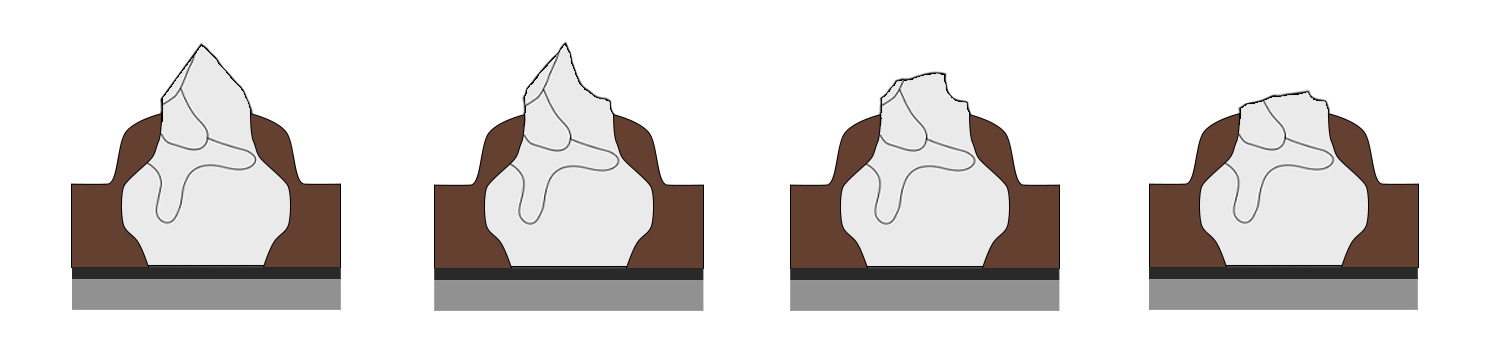
3. ábra. A korundszemcsék kopása - ék alakú, sarokletes szemcsék, makrokopás/kopás
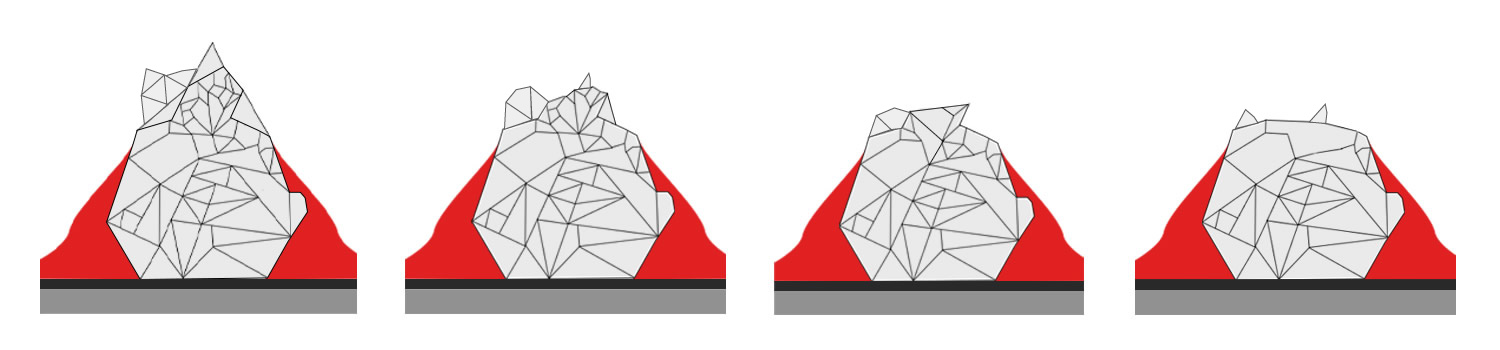
4. ábra. Kerámiaszemcsék kopása – hegyes, éles szemcsék, mikrokopás/önélezés
A szerszám megmunkáló felületén a szemcsék tompulása lassabb vágást vagy lassabb anyagleválasztást eredményez csiszoláskor, a betétszerszám és a megmunkálandó anyag nagyobb mértékű felmelegedését, a betétszerszám nagyobb igénybevételét és végső soron nagyobb energiaigényt a vágás/csiszolás során.
A hagyományos korund és a kerámia csiszolóanyagokból készült betétszerszám teljesítményének összehasonlítása
Az összehasonlításhoz kiválasztottuk a legkelendőbb 125x1,0 mm-es AS-30 Classic korundból készült vágótárcsánkat, és összehasonlítottuk a teljesítményét az új AX-30 Ceramic vágótárcsánkkal. Azonos tesztnek vetettük alá őket a tesztberendezésünkön (5. ábra), a vágandó anyag 16 mm átmérőjű szerkezeti acél volt, a betétszerszámot egy HERMAN WX-12501 sarokcsiszolóba (1000 W) fogtuk be, és a teszt során a sarokcsiszoló előtolási sebességét a vágandó anyagban 3 mm/másodperc értékre állítottuk.
A két különböző tárcsa vágási tulajdonságainak durva összehasonlításához elegendő, ha mindkét tárcsával hússzor vágjuk a fent említett acélt. Mivel ebben az esetben két, egymástól jelentősen eltérő tulajdonságokkal rendelkező termék pontos összehasonlítását kívántuk elvégezni, a következőképpen folytattuk a vizsgálatot:
Az első fázisban mindkét szerszámmal 20 vágást végeztünk, a második fázisban pedig további 30 vágást (azaz összesen 50 vágást). Minden egyes fázis után megmértük a vizsgált szerszámok átmérőveszteségét, és kiértékeltük a vágás energiaigényességét. Végül a vizsgált szerszámokat ugyanezzel a módszerrel a teljes elhasználódásig teszteltük (a teljes elhasználódás a mi vizsgálati körülményeink között a 91 mm* maradék betétszerszám átmérő elérését jelenti), hogy lássuk, hány vágást képes a betétszerszám az élettartama alatt elvégezni.
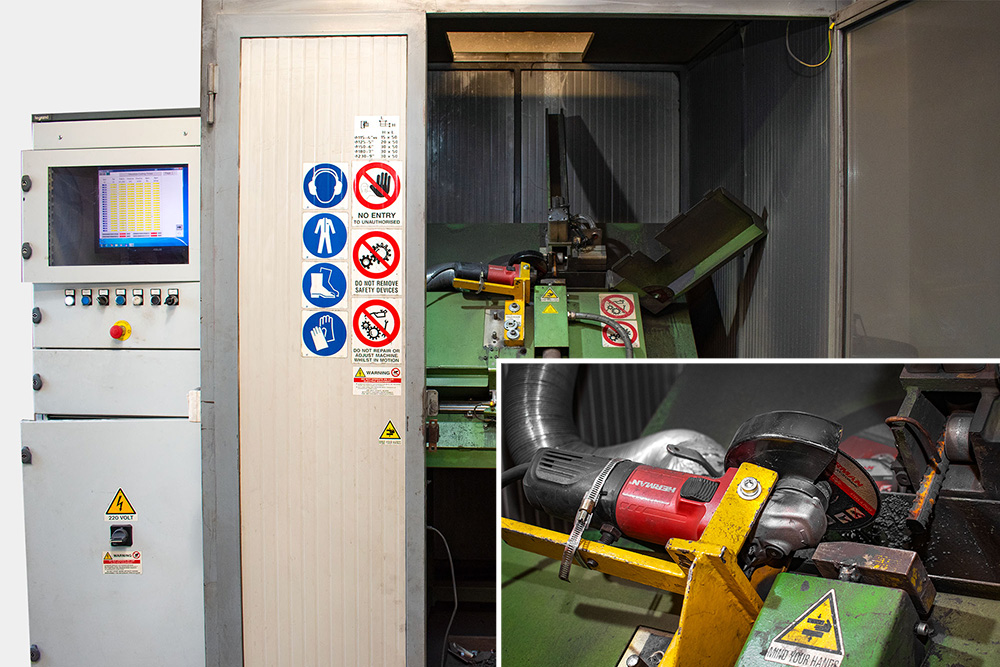
5. ábra. A vágótárcsákat tesztelő berendezés
* A sarokcsiszolónk mechanikai kialakítása és a vizsgálóberendezésben való rögzítése lehetővé teszi legalább 91 mm átmérőjű vágótárcsa használatát, ezért ezt az átmérőt tekintjük határértéknek a mi körülményeink között. Más körülmények között, más méretű anyagok vágásakor, más sarokcsiszoló használata esetén a teljesen elhasználódott tárcsa átmérője lehet kisebb, de lehet nagyobb is.
A vizsgálati eredményeket az alábbi 1. számú táblázatban foglaltuk össze. Minden mért érték három darab tárcsa tesztelésének átlaga az egyes típusokból.
A vágótárcsa típusa | HERMAN AS-30 Classic | HERMAN AX-30 Ceramic |
Csiszolóanyag | korund | kerámia |
Új tárcsa átmérője (mm) | 125,0 | 125,0 |
Az új tárcsa súlya (g) | 33,0 | 34,0 |
A tárcsa maradék átmérője 20 vágás után (mm) | 119,4 | 123,5 |
A tárcsa maradék átmérője 50 vágás után (mm) | 98,0 | 120,5 |
Átlagos vágási áramerősség (A) | 4 | 2,9 |
A tárcsa ára (Ft) | 338 | 756 |
A teljes elhasználódásig tartó vágások száma | 82,2 | 216,1 |
Ár / 1 vágás (Ft) | 4,11 | 3,50 |
1. táblázat. Az összehasonlító vizsgálat eredményei
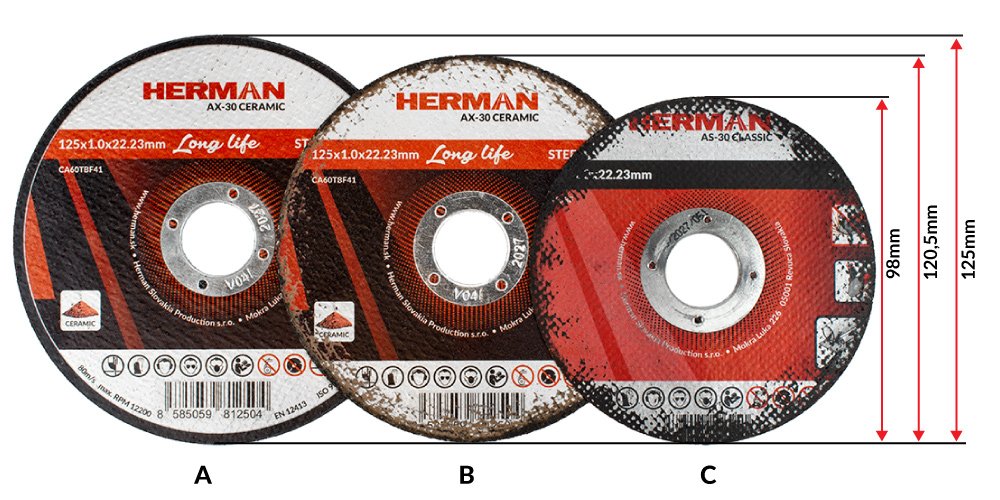
6. ábra. A korund (C) és a kerámia (B) vágótárcsa kopása az
új (A) tárcsahoz képest 50 vágás után 16 mm
átmérőjű szerkezeti acél vágása
A jobb áttekinthetőség érdekében a 6. ábra a kétféle típusú tárcsa kopásának összehasonlítását mutatja 50 vágás után.
Ha a betétszerszám kiválasztásának egyetlen kritériuma a vágásonkénti ár, akkor gyakorlatilag lényegtelen, hogy melyik szerszámot választjuk. A kerámiaszemcsékből készült vágótárcsa kb. 2,5-szer hosszabb szerszámélettartammal rendelkezik (6. ábra), mint a hagyományos korundból készült tárcsa, de 2,5-szer drágább is.
Meg kell azonban említeni, hogy egy vágás költségét egy egyszerűsített módszerrel számoltuk ki: a szerszám árát elosztottuk az élettartama alatt vele elvégezhető vágások számával.
Nem vettük figyelembe például a vágás közbeni energiaköltségeket, a munkabér költségeket stb. pedig ezek nagyon fontos paraméterek. Vegyük észre a kéziszerszám áramterhelése közötti különbséget: 4,0A a hagyományos tárcsával történő vágás esetén vs. 2,9A a kerámia tárcsával történő vágás esetén. Már első ránézésre is 37%-kal kevesebb. A valóságban azonban a különbség még jelentősebb, mivel maga a sarokcsiszoló 1,5A-t vesz fel üresjáratban, vágási terhelés nélkül. Tehát maga a vágás során felvett áram reálisan 2,5A, amikor hagyományos tárcsával vág, szemben az 1,4A-al, amikor kerámia tárcsával vág, vagyis 78%-kal kevesebb. Mit mondanak ezek a számok? Az energiamegtakarítás tekintetében az első szám igaz - 37%-ot takarítunk meg. A második szám a munkakényelemről szól, és aki napi segédeszközként sarokcsiszolót használ, az jól tudja, mennyivel kényelmesebb egy olyan szerszámmal dolgozni, amely könnyebben megy bele a vágásba. A munkát végző nem fárad el olyan gyorsan, és a munka minden szempontból hatékonyabb.
Ha ezeket a tényezőket figyelembe vesszük, a mérleg nyelve a modernebb termék felé billen:
- a kerámiaszemcsés tárcsát nem kell olyan gyakran cserélni az elhasználódása után
- kevesebb hulladékot kell leadni/feldolgozni/újrahasznosítani
- gyorsabb vágás
- kisebb energiafogyasztás: energiaköltség-megtakarítás, kényelmesebb és hatékonyabb munkavégzés a betétszerszámmal
Ezeknek a tényezőknek a vágásonkénti árra gyakorolt hatása nem elhanyagolható, ugyanakkor nem könnyű számszerűsíteni. Egy későbbi cikkben részletesebben foglalkozunk majd ezzel a témával.
Nem minden kerámia ugyanaz a kerámia
A kerámia csiszolóanyagoknak számos fajtája létezik, a legelterjedtebbek és legolcsóbbak az IceCut vagy a BlueCut kereskedelmi nevek alatt ismertek. A mi csiszolószerszámaink is ebből a szemcséből készülnek. Az egyes szemcsék szabálytalan alakúak, és minden elterjedt szemcseméretben kaphatók.
Vannak fejlettebb változatok is, amelyeket egységes forma jellemez (PSG - Precision-Shaped Grain), többnyire kis háromszögekről van szó (7. ábra) vagy pontosabban háromszög alapú hasábokról. E csiszolóanyag előállításának technológiája szabadalmaztatott és igényes. Csiszoláskor a szemcsék a háromszög oldalai mentén pontosan hasadnak, így a szemcsék több hasadás után is megmaradnak egyenes oldalúnak és élesnek. Erre példa a 3M által gyártott Cubitron szemcse. Ez a szemcse még jobb csiszolási tulajdonságokkal rendelkezik, mint a szabálytalan alakú kerámiák.
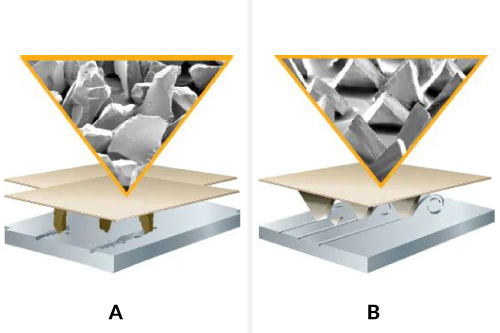
7. ábra. Vágás hagyományos (A) és háromszög alakú (B) kerámia csiszolóanyaggal
Zárszó
Az ügyfél döntésén múlik, hogy hagyományos csiszolóanyagokból készült csiszoló betétszerszámokat használ-e, vagy ad egy esélyt az új, progresszív technológiának. Az évtizedek óta bevált csiszolóanyagok még sokáig velünk maradnak, de az összehasonlító tesztek és a növekvő vásárlói érdeklődés azt mutatja, hogy a kerámia csiszolóanyagok fokozatosan utat törnek maguknak. Valóban erősek és hatékonyak, de mint említettük, ezeknek a csiszolóanyagoknak számos változata létezik, és jelentős különbségek is vannak közöttük. Ráadásul a kerámia csiszolóanyagokat nagyon gyakran kombinálják a hagyományos csiszolóanyagokkal különböző arányban a csiszoló betétszerszámokban - főként azért, hogy bizonyos kompromisszumot érjenek el az ár és a betétszerszám teljesítménye között. Már 20%-os kerámia csiszolóanyag hozzáadása a korundhoz észrevehető teljesítménynövekedést eredményez. Teljesen más azonban egy prémium kategóriás szerszámmal dolgozni, amely 70% (szélsőséges esetben akár 100%) kerámia csiszolóanyagot tartalmaz. Sok eladó a „CERAMIC” stb. feliratot teszi a termékére, de ritkán tudják, hogy milyen típusú kerámia csiszolóanyagot használnak, és milyen arányban keverik a hagyományos csiszolóanyagokkal. Cégünk maga gyártja a csiszoló betétszerszámait, így teljes kontrollunk van ezen paraméterek felett.
Kulcsszavak: kerámia csiszolóanyagok, korund, csiszolás, anyagleválasztás, teljesítmény összehasonlítás, csiszolóanyag tesztelés
Források:
A HERMAN cég belső műszaki és oktató dokumentációi
Josef –
Dobře zpracovaná spousta zajímavých a neznámých fakt.
Sok érdekes és ismeretlen tény jól előkészítve.
Lefordítani a szöveget Eredeti szöveget mutatniVajna József –
Igényes és tartalmas cikk.
Nyilvánvalóan ilyen munkához védőfelszerelést és aktívszenes maszkot használunk. Ugyanakkor mivel a szellőzés nem a legjobb (mert mi pl lakott lakások egy-egy zárt helyiségében dolgozunk a vágások során, fontos lenne tudni olyan érzékelhető és a komforttal összefüggő dolgokról is mint a munka környezetét terhelő szag, káros anyag, szálló por. Felteszem, hogy a kerámia mivel ezek szerint lassabban is kopik, alacsonyabb marad a hőmérséklet, jobb eredményt ad vágások során.
Kántor Sándor –
Mindig örülök a technológia fejlesztésének. A cikk tiszta, világos érthető. Nálunk a köszörülés, szinte mindig a befejező művelet. A köszörülés koronázza meg az alkatrészt. Szívesen kipróbálnánk a korongokat sík és palást köszörülésben is amennyiben már gyártják őket. Nálunk a járatos méretek:
D 350 x 40 x d40
D 350 x 40 x d 127
D 300 x 40 x d 76
D 500 x 75 x d 305
Az alkatrészek ötvözött szerszámacélból készülnek, 60 -62 HRC keményre vannak edzve.
Válasz:
Kedves Kántor Úr, köszönjük a cikkünkre adott pozitív válaszát. Ami a kérését illeti, sajnos a síkköszörüléshez szükséges korongok nem szerepelnek a szállítási programunkban. Ha másra lenne szüksége, pl. vágó- és csiszoló korongokra, akkor szívesen kiszolgáljuk Önt.
Jozef –
Veľmi dobrý článok,detailne popisujúci vyber rezných a brúsnych kotúčov do uhlových brúsok.
Nagyon jó cikk, részletesen leírja a sarokcsiszoló vágó- és csiszolótárcsák kiválasztását.
Lefordítani a szöveget Eredeti szöveget mutatni